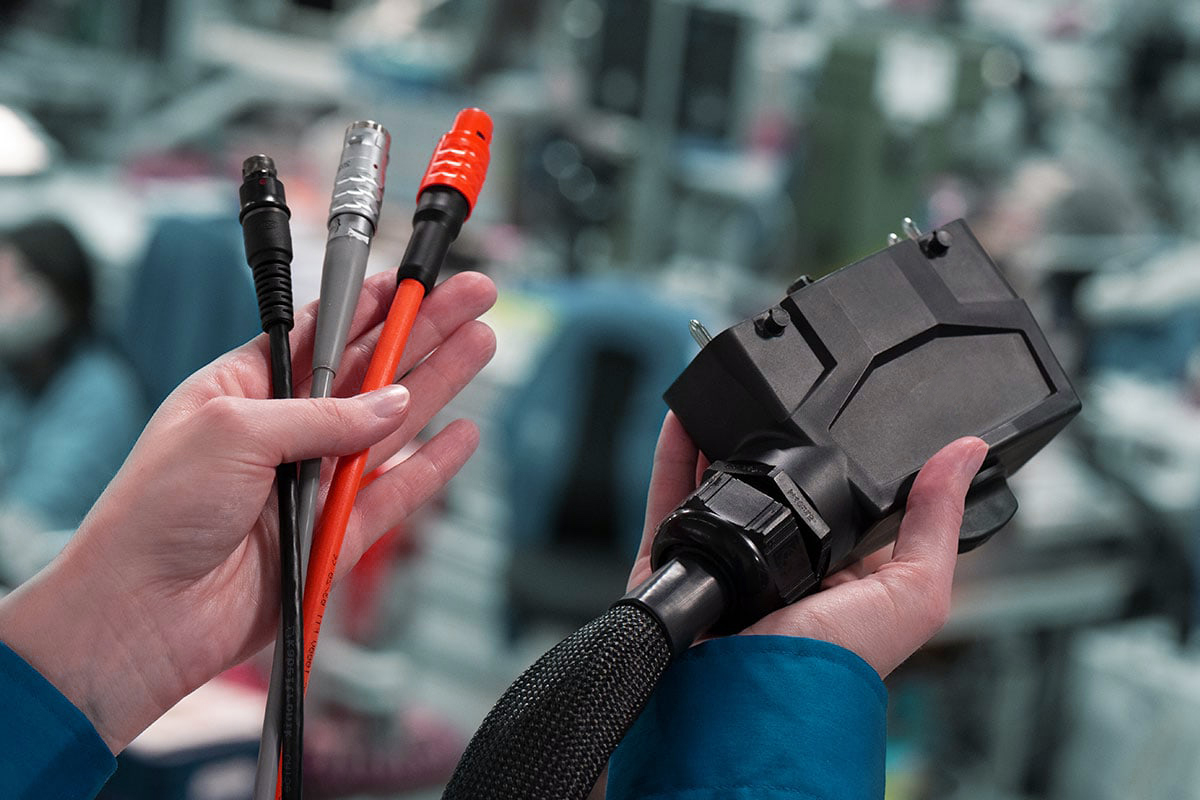
Custom Cable Assemblies: The Invisible Link Between Technology and Market
1. The Lifeline Hidden in the Details
You probably never stop to think about it, but every time you charge your phone, start your car, or watch machines hum in a factory, custom cable assemblies are quietly working behind the scenes. Like the veins and arteries in a human body, they precisely carry power and signals, yet rarely get the spotlight. These unassuming connectors are the backbone that keeps everything from smart homes to aerospace equipment running smoothly. Without them, even the most advanced technology would be nothing more than an empty promise.
2. The Many Faces of Cable Assemblies
Cable assemblies come in various forms, each suited to different needs.
Standard assemblies are like Lego blocks—versatile, cost-effective, and designed to meet general requirements. They serve well in many everyday applications where customization isn't critical.
Custom assemblies, on the other hand, are tailored like a bespoke suit. They are engineered to handle special conditions such as high temperatures or electromagnetic interference. For example, cables inside medical devices must be flexible enough to bend easily while also shielding sensitive electronics from interference.
Then there are hybrid assemblies, which combine the strengths of fiber optics and copper cables to meet complex transmission demands. This blend allows for high-speed data transfer alongside reliable power delivery, a necessity in many cutting-edge fields.
3. Why Manufacturers Are Willing to Pay for Customization
A robot manufacturer once shared a telling experience: "Standard cables kept breaking at the joints, but after switching to custom assemblies, the lifespan tripled." This hidden value of customization is what drives many to invest.
-
Performance matching: For instance, 5G base stations require ultra-low-loss connections to maintain signal integrity.
-
Space optimization: Automotive wiring harnesses are designed to fit tightly within compact engine compartments.
-
Risk mitigation: Offshore oil drilling platforms demand explosion-proof cable designs to ensure safety.
These examples show how custom cable assemblies do more than just connect—they solve real-world problems.
4. Challenges and Opportunities Side by Side
Sector | Key Needs | Typical Challenges |
---|---|---|
New Energy Vehicles | High-voltage, high-current transmission | Balancing lightweight design with heat dissipation |
Industry 4.0 | Real-time data exchange | Designing for mechanical vibration resistance |
Medical Imaging | High-precision signal fidelity | Compatibility with sterilization processes |
The global custom cable market grew by 12% in 2023, reflecting how industries are increasingly relying on tailored solutions to overcome these challenges.
5. How Great Cable Assemblies Are Made
Precision is everything. Laser measurement tools ensure millimeter-level accuracy in production, critical when even a tiny misalignment can cause failure.
Testing goes beyond the lab. Assemblies undergo simulated extreme environments, cycling between -40℃ and 85℃ to verify durability under real-world conditions.
Collaboration is key. OEMs and suppliers work together to build "product gene libraries," such as databases of pre-installed waterproof connectors, speeding up design and ensuring consistency.
6. Conclusion
Stanford Optics has proven over 20 years that producing a quality cable assembly is a team effort involving materials scientists, engineers, and installers alike. As their slogan says, "We don't just sell cables—we build highways for your power and data."
This commitment to craftsmanship and collaboration is what turns simple wires into the vital lifelines of modern technology.